MilliporeSigma Creates a Central Hub for Testing Data
5 min read
SITUATION
A leading supplier to the global life science industry, MilliporeSigma relies on rigorous packaging testing to support the safe and convenient handling of chemical products. With hundreds of packaging configurations, the test lab needed a solution to standardize and centralize configuration data and test results, while supporting compliance with industry regulations.
SOLUTION
The test lab implemented a Laserfiche-driven solution for testing data, called STARS (Scheduling, Testing and Reporting System), as a centralized hub to input configuration and testing information in a standardized way, facilitate calculations of testing formulas, collect reviews and approvals, and generate reports to be shared organization-wide.
RESULTS
The Laserfiche-driven STARS solution has cut the time it takes to review and approve testing data and generate reports by 85%, while eliminating opportunities for manual error and increasing data transparency across the organization. As a result, lab testing employees have reclaimed time to explore new packaging materials and reduce response times to service tickets.
MilliporeSigma is the life science business of Merck, which offers best-in-class products for pharmaceutical development and manufacturing. With a portfolio of more than 300,000 products focused on scientific discovery, biomanufacturing and testing services, the company is a leading provider of state-of-the-art tools, services and expertise to scientists and researchers performing experiments and engineering new products..
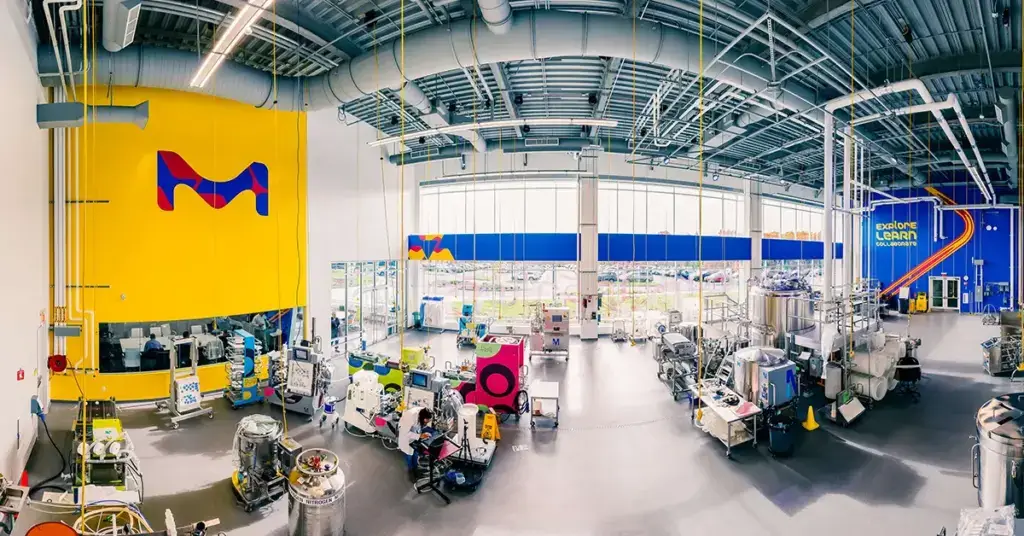
As an organization committed to health and safety in a highly regulated industry, MilliporeSigma relies on rigorous testing of its packaging to support the safe and convenient handling of products. With more than 700 packaging configurations, the company’s test lab needed a solution to standardize and centralize configuration data and test results, while supporting compliance with industry regulations.
“We had a number of applications that we had pieced together to create a tracker,” said Ruth Winters, senior project manager at MilliporeSigma. “There was a lot of manual effort, and so we saw opportunity to build a more efficient, more centralized and standardized process.”
The test lab reached out to Laserfiche channel partner CTaccess and discovered a solution that met the organization’s requirements in Laserfiche. The team built and implemented a system, called STARS (Scheduling, Testing and Reporting System), which now acts as a centralized hub to input configuration and testing information in a standardized way, facilitate calculations of testing formulas, collect reviews and approvals, and generate reports to be shared organization-wide.
Centralizing and Standardizing Testing Data
The main goal for the new solution was to better manage testing data. “We ship dangerous goods, which require packing materials and configurations that must be tested,” said Winters. “We have packing instructions that go along with those as well. And we have over 700 configurations which must be tested on a regular cycle.”
With the test lab’s legacy process — comprising a combination of spreadsheets, Word documents, Microsoft Teams tasks and SharePoint — there was little control over the data that packaging testers could input, and not enough visibility into any changes to the information. The testing reports that were developed were not standardized, often using varying wording or technical terminology that made reviewing them time consuming. In contrast, the new, Laserfiche-driven STARS process is kicked off with a Laserfiche form, which packaging engineers and technicians use to capture testing information in a standardized manner.
Laserfiche Forms is the foundation of the STARS system. Forms enable packaging engineers to update information within MilliporeSigma’s databases that comprise all the information they need to know about packing and configurations — including information about parts that belong in a configuration, the type of configuration, instructions for packing, etc. — and track that data and how long it’s been since it’s been tested.
A Laserfiche workflow automatically notifies staff when configurations need to be tested, and testers use a Laserfiche form that can be accessed from a mobile device, making it easy for them to input data while testing. (Previously, testers would print out the information and handwrite the information, which introduced opportunity for human error and illegibility.) During tests, testers can also take photos with their mobile devices which are automatically uploaded into the form.
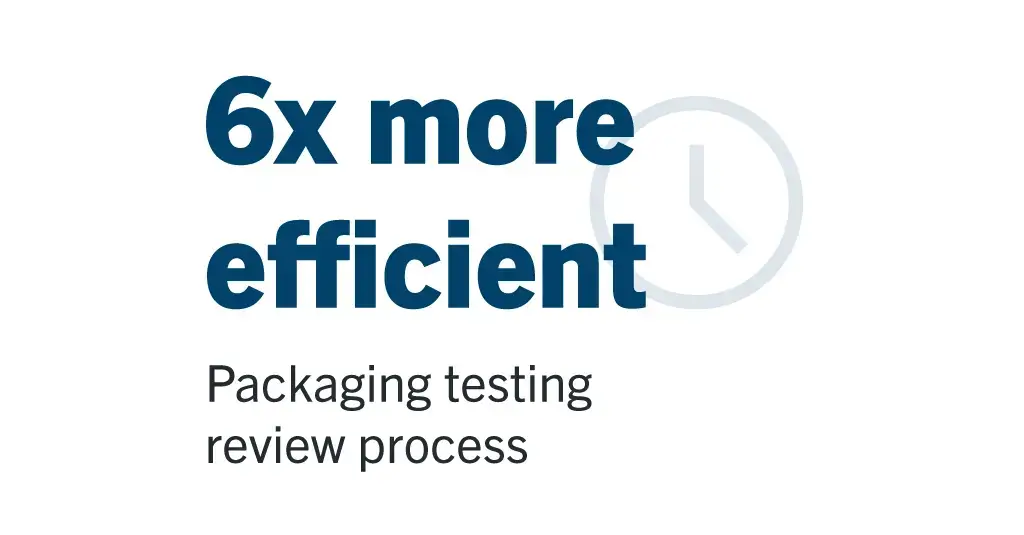
“Today, the data that comes through STARS is consistent and standardized — forms are complete, and I don’t need to manually key in numbers or do calculations,” said Robert Emerson, senior packaging engineer at MilliporeSigma.
“At the same time, Laserfiche gives us peace of mind because it doesn’t allow anyone to go into the system and make changes, or perhaps inadvertently make a change, without my knowledge. Core information like packaging components and instructions must follow specific parameters. That’s so important for the organization, and a big help to me.”
Once testing is complete, Laserfiche Forms auto-formats all of the data and completes backend calculations — used to be done manually — for packaging testing reports. Critically important information like who did the testing, when it was done, what tests were completed and who approved them is all also included in the report.
Managing testing data in a consistent way, in a standardized structure where information is easily navigated and retrieved also streamlines compliance and audit procedures. The test lab has already received positive feedback from DOT auditors and MilliporeSigma’s compliance team.
“In the world of dangerous goods, these reports are critical,” Emerson said. “Laserfiche and STARS is the central hub for our whole testing program, and we are the primary testing lab domestically for Millipore Sigma.”
“We are audited by the DOT,” Winters added. “There are also audits where we need to show how packages were tested, so we need access to test reports for configurations. Or, if there is ever an incident, we need to be able to track and easily show how everything is tested. STARS allows us to pull those reports, show that we did our due diligence and present the supporting information that proves it.”
Reclaiming Time for Innovation
Beyond standardized data management, the benefits of Laserfiche at MilliporeSigma have also included impressive time savings for test lab staff.
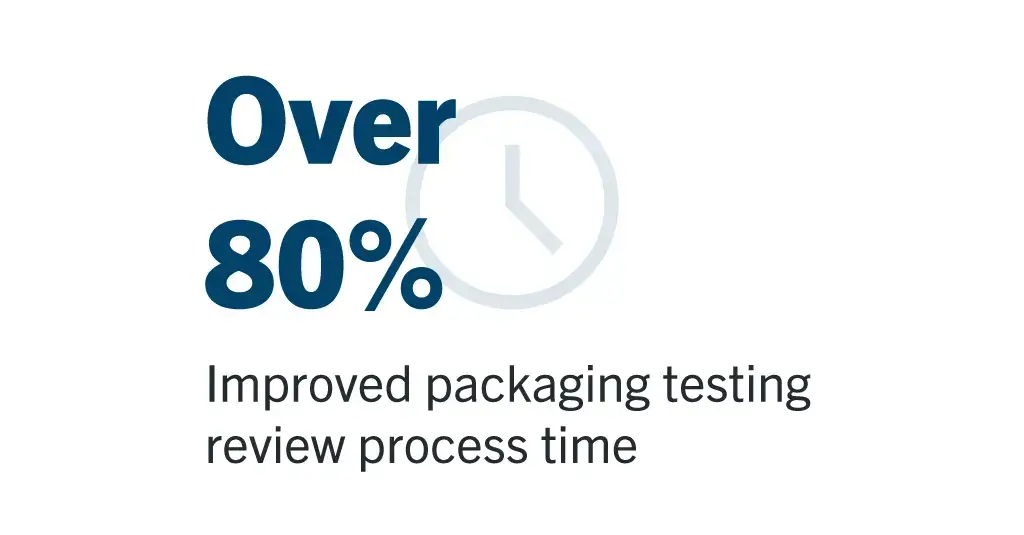
Because STARS eliminates much of the manual intervention that was involved in the legacy testing reports process, Emerson has been able to shorten the time it takes to review, assemble and approve a report from about an hour down to 10 minutes — an improvement in efficiency of over 80%.
Because of the volume of configurations being tested (the lab could have up to 50 test reports in a month), the increased efficiency has been transformative for the test lab. “Today, the process is so much more streamlined, which has freed up time to catch up on other activities, different projects and focus areas,” Emerson said. “If we want to investigate new materials, we have the opportunity. We’re able to explore more with that time. That door is opening — and we’ll continue to open the door to more exploratory activities, more research, the ability to investigate the things that we think are cool in packaging that we just didn’t have time for before.”
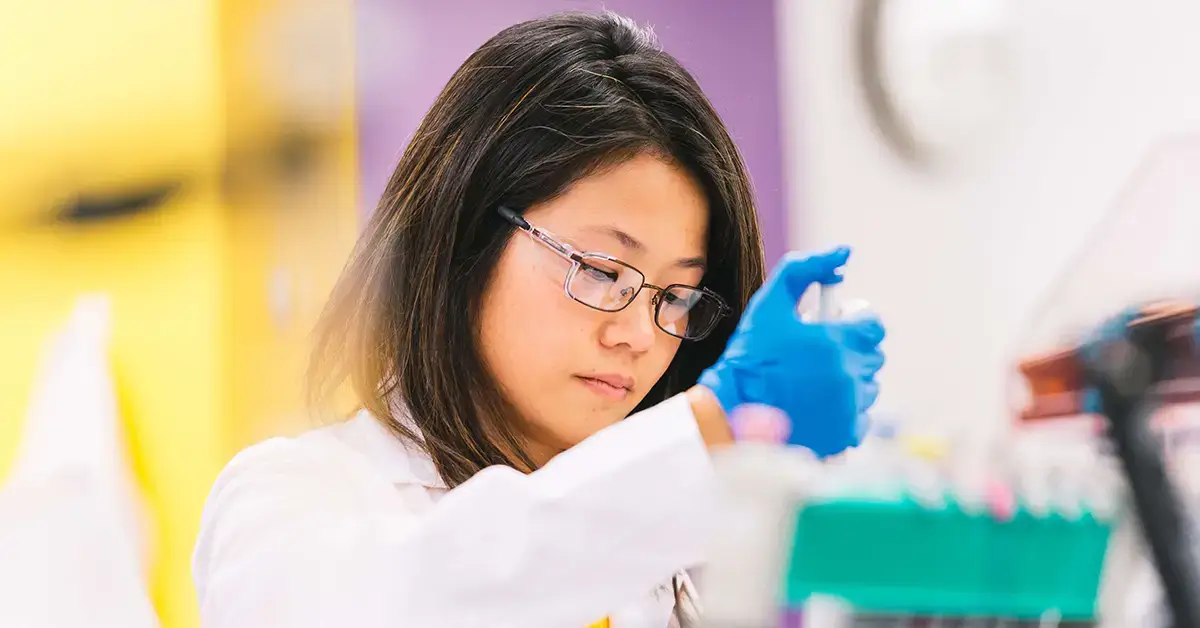
Additionally, Emerson explained that his team has been able to address service tickets more quickly for stakeholders and internal customers. Meanwhile, the new Laserfiche system will be much easier for new team members to learn, supporting faster onboarding.
“There is a lot of opportunity now that we’ve established a platform via Laserfiche,” Emerson said. “We’ve got a system that we’re all working under, and everything is straightforward and intuitive. It’s a big leap over where we were just four or five years ago. And we’ll continue to optimize and build upon that success.”